聚乙烯接口皮子是一種廣泛應用于塑料管道系統中的連接部件,主要用于確保不同管道之間的牢固連接,避免泄漏,并提高系統的使用壽命。其制造工藝與技術直接影響到性能和使用效果,本文將對其制造工藝進行解析。
聚乙烯接口皮子的制造過程一般包括材料選擇、模具設計、注塑成型、焊接處理等幾個關鍵環節。
一、材料選擇
原材料通常采用高密度聚乙烯(HDPE),因其具備良好的抗壓、抗腐蝕、耐磨損等特性。此外,高密度聚乙烯具有較高的機械強度和較低的線膨脹系數,使得其在較大溫度變化和壓力條件下能夠保持穩定性能。
二、模具設計
在制造時,首先需要根據設計要求進行模具的設計。模具設計要求具有良好的流動性,能夠使聚乙烯材料在加熱和注射的過程中均勻填充到模腔內,確保產品的尺寸精度與質量。
三、注塑成型
注塑成型是制造聚乙烯接口皮子最常見的方式。該工藝包括加熱、注射、冷卻等步驟。具體流程如下:
1、加熱:聚乙烯顆粒被加熱至熔融狀態,此時,聚乙烯的粘度降低,具備了流動性。
2、注射:將熔融后的聚乙烯通過注射機的噴嘴注入模具中,模具內的形狀會決定最終外形和尺寸。
3、冷卻:聚乙烯在模具中冷卻后固化,形成所需的形態。冷卻時間需要根據模具的尺寸、聚乙烯的冷卻速率等因素進行合理控制。
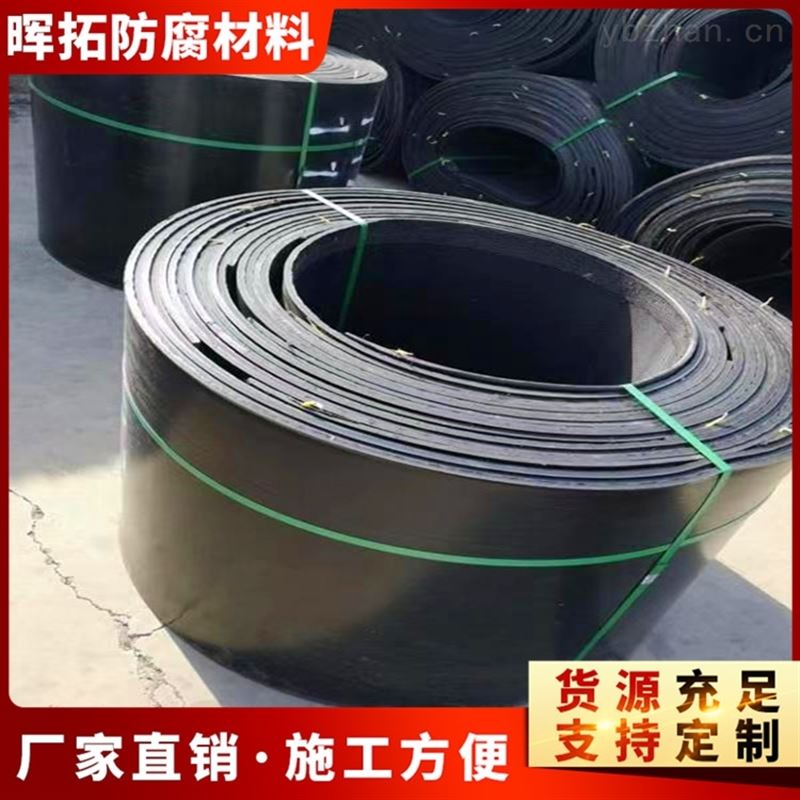
四、焊接與組裝
完成注塑成型后的通常還需要進行后續的焊接或組裝,以確保各部件之間的牢固連接。最常見的焊接技術包括熱熔焊接和電熔焊接。
1、熱熔焊接:通過加熱接頭部分,使聚乙烯材料達到熔融狀態,然后將兩端的管道接口皮子進行對接,冷卻后形成穩定的連接。該工藝廣泛應用于中小型聚乙烯管道的連接。
2、電熔焊接:采用電熔接頭,通過通電加熱金屬絲,使接頭處的聚乙烯材料熔化,達到連接目的。該工藝適用于較大尺寸和高壓力環境下的管道連接。
聚乙烯接口皮子的制造工藝涵蓋了從原材料選擇、模具設計到注塑成型及焊接處理等多個環節。通過不斷優化這些工藝,能夠生產出質量更高、性能更優的產品,為管道系統的安全運行提供保障。